Shop
How Chart Industries Helps Breweries Treat Wastewater
Chart Industries new technology helps breweries be more safe and sustainable.
This is a paid, sponsored post presented by Chart Industries.
Sustainability has become a tenet for many breweries, striving to reduce their carbon footprint and their impact on the environment. Unfortunately, brewing can be a wasteful process, particularly when it comes to disposing of wastewater. According to the Brewers Association, it takes seven barrels of water to make a single barrel of beer.
To help breweries reach their sustainability goals, the innovative Chart Industries invested in the leading technology for improving energy and water efficiency at a brewery, especially when it comes to the byproducts of brewing. With more and more breweries interested in refining their brewing methods, Chart Industries’ approach to treating wastewater stands to change the game.
What Is Chart Industries?
Following the tagline “cooler by design,” Chart Industries is a supply company that specializes in all things cold: think heat exchangers and cryogenic liquid storage of a variety of industrial gasses – from carbon dioxide and oxygen used in water treatment and industrial processes, to natural gas and hydrogen to power society’s transition to a low-carbon economy. In addition to producing top-of-the-line brewing equipment, they’ve also taken a stand as an equitable and inclusive business.
In the beverage industry specifically, Chart Industries has made a name for itself by providing highly accurate LN2 dosing equipment that uses liquid nitrogen to eliminate dissolved oxygen in beverages and pressurize containers reducing packaging material, waste, and the carbon footprint of products.
More recently, Chart Industries leveraged its expertise in carbon dioxide to help breweries treat water in a safe, effective, sustainable, and cost-efficient way.
How Do Breweries Handle Wastewater?
As one of the four main ingredients in beer, water often composes up to 95 percent of the liquid in your can or glass. But, brewing requires far more water, often reaching that aforementioned ratio of seven barrels of water to only one barrel of beer — and this does not even include the estimated 672 gallons of water used in the rest of the supply chain before the raw materials and other inputs arrive at the brewery.
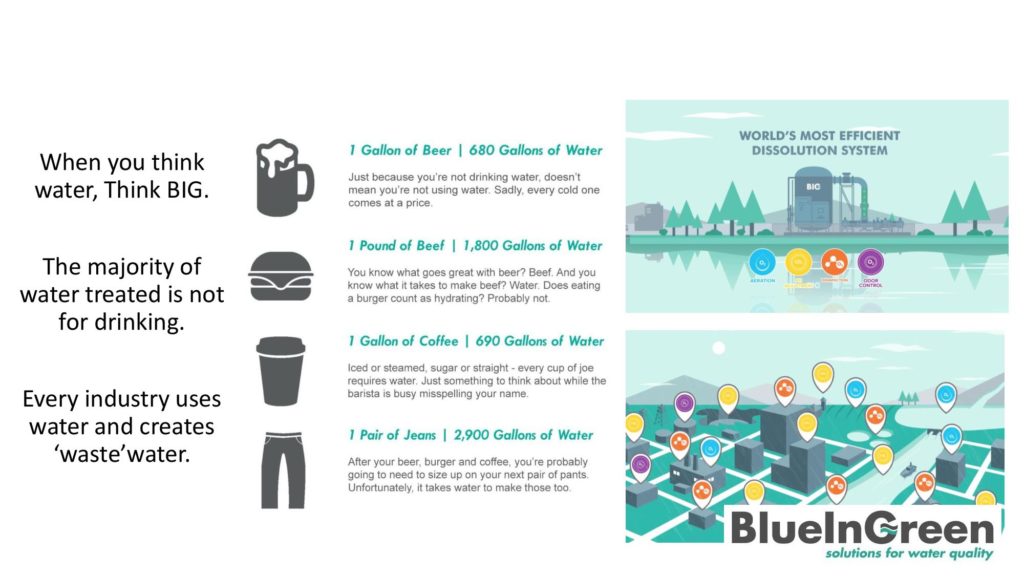
Photography courtesy of Chart Industries
The extra water that doesn’t make it into your beer is considered wastewater, or effluent. In general, brewing creates wastewater that has a high pH and is low in oxygen.
In many communities, municipal water treatment plants have specific requirements for the effluent. Breweries are often required to adjust the pH to acceptable limits and remove solids that have settled into the water as a byproduct of the brewing process. Most craft breweries pre-treat wastewater to address these issues prior to discharging to municipal collection systems for treatment at the local wastewater treatment plant. If these requirements are not met, the brewer is often subject to surcharges and/or fines.
“Historically, breweries and others in the food and beverage industry have adjusted the pH of their effluent with chemicals like sulfuric acid,” says Richard Rosik, Sales Manager at Chart Industries. “By dosing wastewater with a strong acid you lower its pH.”
The problem? Chemical treatment methods – such as the use of sulphuric acid to control pH – can be extremely expensive and their use is often associated with real and perceived risk to the health and safety of employees. Using sulfuric acid to manage the pH of wastewater can also be harmful to the conditions required for the successful biological treatment of the effluent at the local wastewater plant, which must maintain a relatively neutral pH and an aerobic environment to sustain a healthy population of microbes that consume the solids.
How Is Chart Industries Impacting the Beer Industry?
In November 2020, Chart Industries acquired BlueInGreen LLC, a water cleantech company and dissolved-gas expert that provides engineered solutions for water treatment and industrial process applications. The water solutions company provides efficient methods for pH adjustment, aeration, oxidization, and odor control.
The partnership combines Chart Industries’ expertise in cryogenic gas storage with BlueInGreen’s CDOX® dissolution technology, the most efficient method of dissolving gases in liquids. Known as Chart Industries’ CO2 Storage and Feed System, the technology lets breweries safely and efficiently introduce whatever gas they choose into wastewater, whether its carbon dioxide to control pH or oxygen to maintain an aerobic environment and a healthy populartion of microbes.
“Our respective products have always been complementary to the other’s value proposition,” says BlueInGreen Chief Marketing and Business Sustainability Officer Tyler Elm. “Now — together, with an integrated, whole solution — we are even better positioned for success in a world challenged by unprecedented demand for energy, food, fiber and water, all of which is compounded by the effects of climate change.”
Rosik agrees: “[This partnership] is a good marriage [because] we’re now able to give customers a value proposition that wasn’t there before and a solution they may not have heard of.”
How Does the Chart Industries System Create More Energy Efficient Brewing Process?
“While relatively new to the brewing industry, the global trend in water treatment is to manage pH with carbon dioxide in place of sulphuric and other strong acids,” notes Rossik. “Our gas-dissolution systems provide an innovative solution — dissolving carbon dioxide in the wastewater to produce a weak carbonic acid on demand. It’s a fully automated process that provides more precise dosing and, nobody ever has to transport, store, or handle an acid. And, since carbon dioxide gas commonly used by breweries for a variety of applications, brewers can leverage the use of CO2 across a variety of processes.”
In 2012, BlueInGreen pioneered the use of CDOX® technology to control the pH of wastewater in the food industry with one of the nation’s largest dairy companies and has expanded to the mining, fertilizer, power, beverage and other industries as well. It’s also become firmly established in municipal drinking water applications throughout the US.
Using carbon dioxide in place of strong acids delivers the winning value proposition of addressing both the safety and the economic issues of using sulphuric or other strong acids for managing the pH. The benefits of the CDOX® system – safer, more precise dosing resulting in better treatment – are supported by a strong business case driven by the cost difference of the underlying commodity – sulphuric acid relative to carbon dioxide.
“Customers report spending about 30% per unit of treatment compared to the costs of using sulfuric acid” notes Rosik. “And this is straight purchase cost, it doesn’t even account for reduced downtime, reduced changeover time, or the reduced risk of manually handling acid feeds and all of the safety protocols that go along with that. Whereas with the CDOX® gas-dissolution system, everything is automated.”
In short, by replacing chemical treatments of sulphuric acid with carbon dioxide produced on-site and on-demand, BlueInGreen’s CDOX® system successfully controls pH at the lowest combination of risk and cost.
But the Chart Industries solution provides value even to breweries who have already embraced the use carbon dioxide for pH control. Currently, most breweries adding CO2 to their wastewater use a static mixer, a steel blade inside of a large tube that creates turbulence as it’s hit with water.
“Imagine you put a rock into a river,” says Rosik. “As that rock hits the water, you see a swirl. It’s essentially doing that inside the pipe. Every little swirl mixes CO2 into the water. It’s very inefficient and wastes a lot of gas, but it’s very cheap.”
The Chart Industries solution bypasses static mixers, instead taking a side stream of water from the brewery’s water line, super concentrating it with CO2, then injecting the hyper saturated CO2 solution back into the water. The technology automatically adjusts the incoming water and CO2 gas to ensure an accurate pH level with any flow rate changes. The Chart Industries method uses smaller pumps and pipes than most current solutions, and eliminates certain infrastructure that can raise material, labor, and capital costs such as deep basins historically needed for fine bubble diffusers.
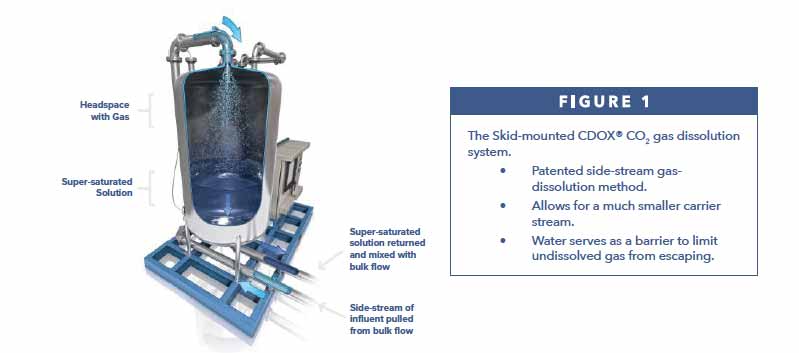
Photography courtesy of Chart Industries
Why Use Chart Industries Technology To Treat Wastewater?
Using Chart Industries and BlueInGreen’s CDOX® Technology to dissolve carbon dioxide or oxygen into wastewater has many advantages: it’s more sustainable, more efficient, safer, and more cost effective. For these reasons, breweries like Samuel Adams have shown interest in adopting the technology.
According to Chart Industries, their technology consumes twenty to forty percent less gas than other alternative gas-dissolution systems for the same level of treatment. And since CO2 is naturally used in the brewing process, many brewers see a bump in their cost savings and sustainability efforts from switching to Chart Industries solution from sulfuric acid.
“If a brewery cares about business sustainability and thinking about reducing, reusing, and recycling their material inputs, they can use the CO2, a byproduct of the brewing process recovered, for their from a wastewater treatment process,” says Rosik. “They can further exploit the CO2 they’re capturing for other processes downstream: carbonation, pH control, and more.”
Although the upfront cost for a Chart Industries solution might be higher, breweries see savings over the long term. In fact, Chart Industries feels so confident about this that – in addition to selling the equipment to breweries outright – customers can adopt the innovation under a Treatment-as-a-Service (TaaS) contract, a program that enables companies to use the CDOX® technology with the financial flexibility of a monthly contract, whether that is to do a side by side comparison for six months to see the tangible cost-saving benefits before purchasing the equipment, or to outsource the entire process, a package that includes the gas storage and dissolution equipment and an award-wining team of engineers and operators to install, service, and support the brewery every step of the way.
“The thing about breweries is, they’re usually not going anywhere soon,” says Rosik. “So on a 15-year life cycle you can see a significant amount of savings.”
Changing from Sulfuric Acid to C02 to Control the pH of Brewery Wastewater
Chart Industries’ new technology is fighting years of entrenched practices in the brewing industry and beyond.
“I think a lot of companies are just so used to using acid they are not aware of the solutions that have come to market in the last 20 years,” says Rosik. “The old technology always worked, but at what cost to the people, the plante, and the pocketbook? And isn’t that the point of innovation — there are always ways to do something better, safe, and more efficiently.”
Carbon dioxide will always be a constant in brewing, and the Chart Industries system allows breweries to leverage their use of CO2 safely, sustainably, and efficiently.
“At the end of the day, we just want awareness of the technology out there,” says Rosik. “I’m really looking at not only saving companies money by using gasses already available [like CO2], and saving on chemicals that aren’t needed, but also doing things differently that are safer for personnel and the environment.”
As more breweries continue to think about sustainability, Chart Industries new technology will be going the extra mile to help breweries brew better beer for its employees, its consumers, its business, and the environment.
This is a paid, sponsored post presented by Chart Industries.
Liked this article? Sign up for our newsletter to get the best craft beer writing on the web delivered straight to your inbox.